|
HISTORY |
FLAG |
MILESTONES |
|
|
|
|
1966 |
FRIGERI was founded by Secondo Frigeri. In 100 sqm. in via Viazzolo Lungo, Guastalla, Italy, the company initially employed three people. Clients were mainly local companies.
|
 |
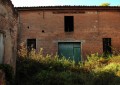 Where it all began |
1970 |
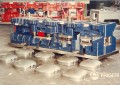 First transfer dies tool set designed and manufactured by Frigeri
|
|
FRIGERI designed and manufactured for MERLONI TERMOSANITARI (now Ariston Thermo, Indesit Group) its first transfer dies tool set for the Cover of an Instant Water Heater. |
1971 |
FRIGERI expanded and moved into 800 sqm. in via Zanardo, Guastalla, later increased to 1.100 sq.m. Staff increased to eight. Clients included leading Italian household appliance companies. |
|
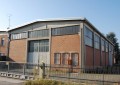 The 1971 Frigeri plant as it appears today |
1974 |
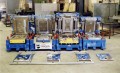 1974 Frigeri Cooking Hob Transfer Dies Tool Set |
|
FRIGERI designed and manufactured for MERLONI (now the Indesit Company) its first transfer dies tool set for a Cooking Hob model (60×50 cm) in various versions, in both cold and stainless steel. |
1975 |
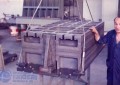 Mr. Frigeri busy at building a perfect die. May 1975
|
|
FRIGERI became the preferred toolmaker for: DE LONGHI, MERLONI (now the Indesit Company) and SMEG. |
|
|
|
|
|
|
1983 |
FRIGERI moved a 2.800 sqm. facility in via Togliatti, Guastalla. Staff increased to twelve. Clients included the main Italian household appliance groups. |
|
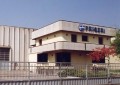 The 1983 Frigeri plant |
1991 |
FRIGERI celebrated 25 years in business. |
 |
|
1993 |
Elisabetta Frigeri became Sole Company Director and thus the running of the company passed to the second generation. |
|
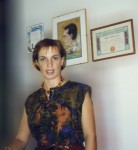 Mrs. Frigeri speaking at a company meeting. June 1993 |
1996 |
FRIGERI expanded adding 2.700 sqm. (5.500 sqm. total) of manufacturing and office space.
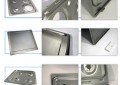 Merloni Indesit Lodz plant parts: combo view
|
 |
FRIGERI started exporting to Poland. For the start-up of the Merloni (now Indesit Polska) Lodz plant, it designed and manufactured tool sets for a built-in 60 cm Cooking Hob, 60 cm Burner Hob Chassis and 90 cm Burner Hob Chassis parts for two Indesit Cooker models. |
1997 |
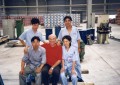 Mr. Frigeri at Client’s Shangai plant. July 1997 |
 |
FRIGERI began exporting to China. It designed and manufactured for the Midea Group 4 tool sets for the Outer Door, Inner Door, Tub Bottom and Ceiling of a 45 cm Dishwasher model. |
1998 |
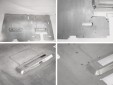 Roca Gaswater Heater Rear Panel Strip Views |
 |
FRIGERI started exporting to Spain. It designed and manufactured for Compañia Roca Radiadores a tool set for the Rear Panel of a Gaswater Heater model. |
2000 |
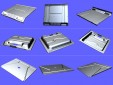 Merloni Electromenager parts: combo view |
 |
FRIGERI started exporting to France. It designed and manufactured for the Merloni Electromenager 3 tool sets for the Bombe Tiroir, Fond de Bombe Tiroir, Habillage Posterieur of a Cooker model. |
2002 |
Technological Revolution
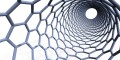 |
|
The FRIGERI technological revolution began, marking the start of three years of continuous investment in new technology and innovation. Key phases were: |
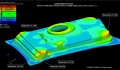 Stamping simulation system |
|
- The engineering department adopted in its routine processes a comprehensive FE-based sheet metal forming simulation framework, a stamping simulation system or virtual press, to simulated stamping of candidate parts both at the RFQ and job stages. |
 3D solid-volumetric design methodology |
|
- The die design process began to be managed exclusively with 3D solid-volumetric design methods. |
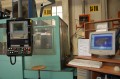 - Company ERP system - Computerization rate of 1,5:1 - Paperless environment - CAM peripheric programming |
|
- An advanced company ERP system was introduced to manage all company processes relating to finished products. - A massive computerisation program started, ending in 2003 at the remarkable average of 1.5 personal computers per employee. - Design and Manufacturing processes were managed in a paperless environment. - CAM programming was transferred from single programmers (central programming) to CNC operators (peripheric programming). |
Quality Management System, according to ISO 9001 standard |
|
- A Quality Management System, meeting ISO 9001 standards, was established. |
2003 |
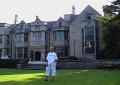 Mrs. Frigeri at Spennymoor, July 2003 |
         |
FRIGERI became Electrolux’s Qualified Global Supplier (QGS) and began to be involved in RFQs from Electrolux plants in Sweden, the UK, Italy, France, Spain, Poland, Switzerland, Germany and the USA.
FRIGERI celebrated its new QGS status with the award of a contract for two series of tools (Cooker Side Panel) for the Electrolux plants in Motala (Sweden) and Spennymoor (UK). |
2004 |
The October edition of STAMPI – PROGETTAZIONE&COSTRUZIONE, one of the two main italian toolmaking magazines, dedicated a seven-page article to FRIGERI, describing it as “a true rarity among Italian small-sized mechanical companies”.
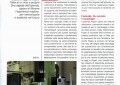 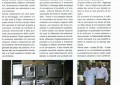 Abstracts from the seven-page article to FRIGERI |
|
The R&D project SPEED (Self-driven Production Expert Environment for Dies) began. The aim was to create a work environment where raw materials and components enter and finished tool sets leave with little or no human intervention. The core knowledge in SPEED (Die Design and Manufacturing) is administered not by humans but by intellixpert systems. The project started with the development of the sw module D-Manufacturing, designed to manage all key manufacturing processes (turning, milling, drilling, edmw, grinding) without expert human intervention. |
2005 |
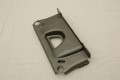 Back Recliner Side Member - Cutting Die and Part Views |
 |
FRIGERI began exporting to Turkey. As subcontractor, it designed and manufactured for the Toyota Motor Manufacturing Turkey three tool sets for the Back Recliner Side Member Outer, Cushion Side Member Outer, Driver Lower Outer Frame parts for a Toyota automotive model. |
2006 |
FRIGERI celebrated 40 years in business. Clients included the main European and International producers of Household Appliances, Lighting, Heating and Air-conditioning, Cars and Industrial Vehicles. In the period 2002-2006 period the company grew by 55%.
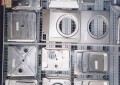 Household appliances totem at Frigeri plant
|
 |
At this point, after 40 years of continuous operation, FRIGERI had designed, manufactured and started up virtually all the metal components and sub-components of the following main household appliances: – Cookers – Ovens – Dishwashers – Washing Machines The reputation of FRIGERI as a vertical and specialized toolmaker in the household appliances market was acknowledged worldwide. |
2008 |
Elisabetta Frigeri was named President of FRIGERI S.r.l. and Roberto Di Zitti Vice-President.
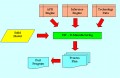 SPEED, DIMES, D-Manufacturing: workflow diagram
|
|
The power and intelligence of the SPEED sw module D-Manufacturing was dramatically improved by hybridization of its code with multiple AI codes (rule-based, frame-based, fuzzy-based). |
2009 |
FRIGERI consolidated its “clean&lean” workforce at 17 people, and increasingly developed and strengthened informal cooperation and partnerships with selected key-companies and professionals. FRIGERI exported about 70% of its production. |
 |
FRIGERI began exporting to Romania. |
2010 |
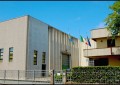 Frigeri plant as it appears today |
|
The SPEED sw module D-Manufacturing reached the alfa release stage. The D-Design sw module and the automatic factory environment design reached operative planning stages. |